Factories relocating from the Mainland face challenges
By Erica Li & Gloria Li
In 1996 Alan Cheung founded a garment manufacturing business, Grandion Industrial. Like many Hong Kong entrepreneurs, Cheung headed north to establish production lines in Guangdong. But three years ago, he launched a project called To Make Locally and relocated some of his factories to an industrial estate in Hong Kong.
The 51-year-old businessman says increasing rent and labour costs as well as the complicated tax system in the Mainland place a heavy burden on manufacturers there and contributed to his decision to move.
Cheung initiated To Make Locally to promote local businesses by using local designers, green production and technology. He hopes to reinvigorate the “Made in Hong Kong” brand by showcasing the comparative advantages of running his business in Hong Kong, including strong copyright protection and a robust legal system.
“When some manufacturers make production prototypes in mainland factories, their products may already be selling on Taobao,” says Cheung, referring to the online shopping platform. “But if we do it in Hong Kong, most companies will feel reassured as the awareness of intellectual property rights protection is higher.”
Cheung says another advantage is that Hong Kong has a free flow of information and the population is in general more aware of the latest fashion trends from other regions and countries, such as Paris and Japan. He says designers in Hong Kong tend to have a more global view.
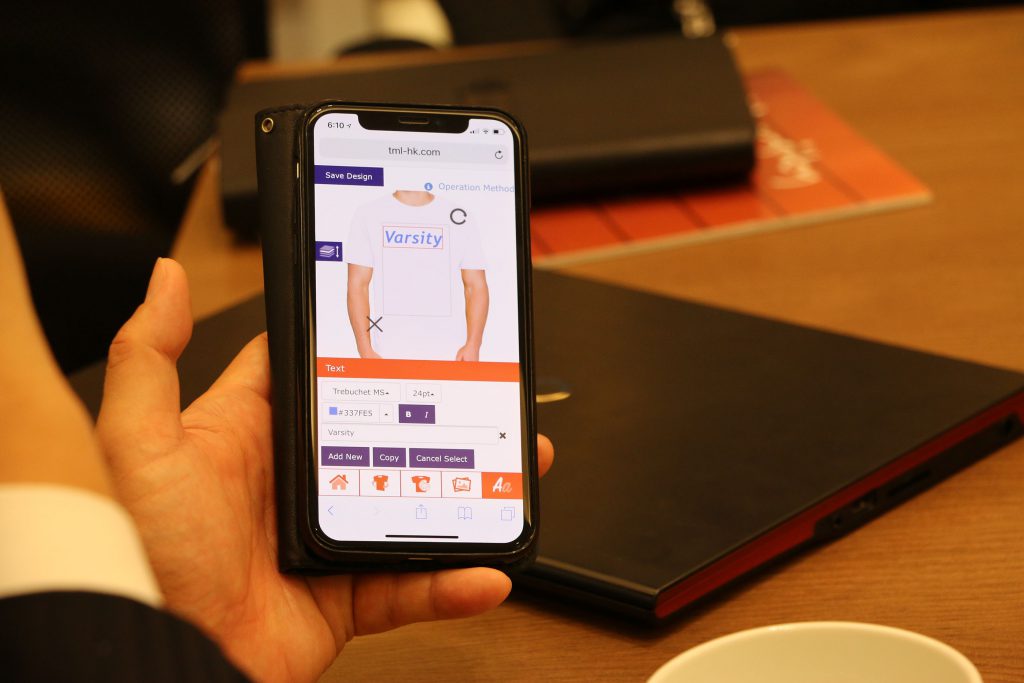
The move to relocate factories to Hong Kong chimes with government plans to diversify Hong Kong’s economy through developing technology and reviving industry. “Re-industrialisation” was highlighted as a potential new area of economic growth in the 2016 Policy Address.
The government hopes the manufacturing industry can contribute up to 5 per cent of Hong Kong’s gross domestic product (GDP), having declined to 1.2 per cent in 2015 from 2.7 per cent in 2006. In 1977, the manufacturing industry accounted for 30 per cent of the territory’s GDP and employed one million workers. By 2016, the number of employees had dropped to around 97,700 despite a larger population overall.
Despite such grand visions, Cheung says it is difficult to transform Hong Kong businesses into high value-added enterprises after relocation, and to develop niche and customised markets. “The problem is we do not have a blueprint to follow,” says Cheung. “We need to learn and to correct our mistakes while running the business.”
Tam Wing-yiu, 56, is the founder of Tool and Mold Hong Kong Limited, a company that produces moulds for a range of toys and healthcare products such as inhalers for asthma relief and electric toothbrushes. Tam once operated factories in the Mainland in a joint venture with an American company but since that contract ended in 2013, he has only set up local factories. He agrees with Alan Cheung that Hong Kong manufacturers have little experience to draw upon because the territory’s factories moved in pursuit of lower costs when the Mainland opened up in the 1980s.
“There is nothing left in Hong Kong. Not any knowledge is left,” says Tam. “The young do not have the chance to do research and development, and Hong Kong gave up its opportunity to be the base of the manufacturing industry.”
Apart from the lack of experience and knowledge, Tam says there is not enough support from the government compared with other countries and this makes local industries less competitive.
“In Germany and Japan, where they have a long industrial history, their government will sponsor half of a machine’s cost,” says Tam. “But in Hong Kong, there is none.”
Limitations of land and space are another issue for companies who are thinking of relocating their production lines to Hong Kong. Hoi Tin Tong Food Limited, a producer of herbal drinks and jellies, has factories both in the Mainland and in Hong Kong. The Hong Kong plant serves the local market and the mainland one caters to Hong Kong, Guangdong and Macau.

Photo courtesy of Christita Ng
Hoi Tin Tong’s general manager, Christita Ng, says most production lines remain in the Mainland to fulfill the great market demand there. The company also has the space in the Mainland to cater to the renewed interest in industrial tourism and can organise tours for visitors to the facility. “The land in Hong Kong is just too expensive,” says Ng. “Our factories in Hong Kong can never be as large as the mainland one.”
In 2016, the government told legislators it did not keep statistics of the number of companies that had relocated to Hong Kong or the number of factories started in Hong Kong by those companies. But in a written reply to lawmakers in May 2017, it said there were 142 companies operating in industrial estates in Hong Kong, with 70 in Tai Po, 40 in Yuen Long and 32 in Tseung Kwan O. Some of the most prominent industries being food and beverages, machinery and parts, as well as biotechnology and pharmaceutical products.
Despite the difficulties and limitations, the Hong Kong Productivity Council (HKPC) says the government has invested over HK$18 billion to promote re-industrialisation in Hong Kong. In a written response, Raymond Shan, principal consultant of Smart Manufacturing and Materials with the HKPC, says that re-industrialisation does not only focus on relocating labour-intensive production lines, but on developing high value-added manufacturing industries and a new business system with the help of innovation and technology.
This is in keeping with the government’s promotion of the development of “Industry 4.0” or the “smart factory” concept. The term originated in Germany and focuses on the use of automation, data exchange and algorithms in manufacturing technology. Shan says that with more overseas customers embracing Industry 4.0, factories in Hong Kong must upgrade their operations.
But this may not align with either the capacity or business models of all Hong Kong manufacturers. Wong Lap-wing is the founder of Universal Engineering Hong Kong Limited which produces back-up electricity generators for buildings and data centres in Hong Kong. Wong has local factories for carrying out design, testing and systems debugging, and both local and mainland factories for product assembly. He says the majority of his production still relies on manpower rather than automation. “Robotics cannot help us,” he says. “Even carmakers still need technicians because there are still procedures machines cannot carry out.”
Wong thinks it is impractical to develop Industry 4.0 in Hong Kong because the costs are too high. Although mass production is possible with the help of automation, he says it would be a waste to invest in robotics because there is not such a high demand for his products in the market. “I am not looking for an expansion of the business. The costs would be so huge if we expanded as monthly expenses would increase,” says Wong. “We might have to close down sooner if we do not have enough orders.”
Lee Ka-man, an assistant professor at the Department of Industrial and Systems Engineering at the Hong Kong Polytechnic University, agrees. Lee says everyone seems to be talking about Industry 4.0 but only has a very vague idea of what it involves.
“To be frank, 4.0 is still a concept,” says Lee. “I have visited some German factories and they said they have not really achieved 4.0 because it requires the internet of things, big data analytics, integration of systems, automation and robotics.”
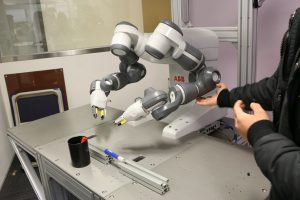
Lee works closely with third-year engineering students on internships with industrial companies. These are supposed to be an opportunity for students to learn more about the sector but because the internships are not compulsory, Lee says, it is hard to recruit both students and companies to take part. Only 20 to 30 percent of teachers contact companies for internships, she adds.
Lee also points out that although there is an Innovation and Technology Fund Project – administered by the Innovation and Technology Commission – which offers two graduate internships related to manufacturing every year, most graduates of the Department of Industrial and Systems Engineering would rather work in the tertiary industries than in the manufacturing industry.
“We hope students can develop their interests in engineering through this project, but it is their choice whether they want to continue with this path in the future,” says Lee.
According to the department’s statistics on graduate employment by sector in 2016, fewer than half of the students who responded to a survey found jobs in the manufacturing sector. With few college leavers willing to join the sector, it is hard to revitalise the manufacturing industry.
Tam Wing-yiu from Tool and Mold Limited is not surprised that few young people want to pursue a career in industry. He says there is an imbalance in society, with most policies benefiting the financial and property markets. “If policies in general are too inclined towards certain sectors, it will make society unhealthy,” says Tam. “Everyone will be the victim in the end.”
Edited by Katie Cheng