Hopes are pinned to the medical use of the technology
By Vivian Lai & Zoe So
There were handicrafts and gadgets galore at the Hong Kong Mini Maker Faire where engineers, inventors and artisans showed off their creations. While many visitors gravitated towards the various robots on display, intent on their pilgrimage to find the perfect geekdom, a handful gathered in a corner of the exhibition hall. Their eyes were fixed on a 3D-printed artificial arm – a simple design, yet a cutting-edge invention – which 31-year-old participant Au Kai-chun was using to try to lift a water bottle.
Born without a left forearm, Au gave up using a traditional artificial arm after a short period of time as a child. “The traditional ones are designed to be durable and heavy, as they assume you will wear it throughout your life,’’ he says. Au has grown accustomed to life without a forearm, but when he came across the idea of a light and stylish prosthesis made by 3D printing, he decided to join a project initiated by the Maker Club as a tester.
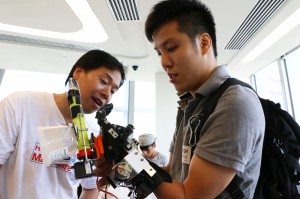
Maker Club is a voluntary group of technophiles, operational therapists and programmers. Inspired by the US-based international network, E-nabling the Future, members decided to help customise artificial limbs using 3D printing technology.
Au explains that designing a perfect prosthesis requires making lots of adjustments. “The traditional mould-making for each adjustment can be very expensive, costing more than HK$100,000 in total … 3D printing is cheap so you can experiment and improve continuously,” he says.
A 3D printer works like a normal printing machine. First, users have to scan an object or send a design blueprint to the printer. The needle-shaped printing head then deposits liquid plastic on the base according to the design. Layer upon layer is laid down until the plastic fuses together and the product takes shape.
Mark Li, one of the organisers of Maker Club, says the cost of producing a prosthesis automated by an electric motor is around HK$2,000, whereas a mechanical one would only cost several hundred dollars to make. So far, Maker Club has helped Au kai-chun and an 8-year-old boy by designing tailor-made plastic limbs for them.
The little boy was born with just a thumb and little finger on one hand, which makes it difficult for him to hold a pen and use an eraser. The doctor says he cannot wear an artificial hand as the traditional design does not fit. “We were touched by this case and so hoped to do something to help him,” says Li whose team designed a tailor-made mechanical fist for the boy. With the mechanical fist, he can control the fingers of his prosthesis to grab objects.
3D printing may bring new hope for disabled people and amputees, as any standardised 3D printer can be used to produce a patient-specific design. However, Tse Chi-yung, a professional prosthetist and orthotist collaborating with the Maker Club, still has reservations about this application of the technology and its limitations. “Amputees can actually get hurt if the prosthetic leg breaks when they are walking,” he says, “I’d hesitate if I had to introduce it to my patients because there’s no official recognition. What if it breaks easily? When it comes to medical equipment, certification is very important!”
3D-printed artificial limbs are lighter and less durable than the traditional ones. Though they are cheap to produce, they are only expected to last for one to two years. Lifting heavy objects or accelerating suddenly could overload and break a prosthesis, leading to safety concerns. There is still a long way to go before hospitals can recognise the use of 3D-printed artificial limbs.
Although 3D printing may seem to be new and cutting-edge, the manufacturing industry has been using this technology for years, especially in the production of toys, jewellery and other small components. Compared to using traditional mould-making and die-casting to mass produce identical objects, 3D printing is more flexible, customisable and design-sensitive.
It has become better known among the general public recently because some local artists have used the technology to make sculptures and artwork, while cheaper, consumer-targeted 3D printers have enabled handicraft workshops to let people have a go at printing their own designs. The biomedical application of the technology remains less well-known and understood.
The Prince of Wales Hospital is one of the earliest medical institutions to use 3D printing as a surgical aid. Dr Tang Ning, a consultant in the Department of Orthopaedics and Traumatology, has pioneered the use of 3D printing technology to perform pre-operation surgical planning. After scanning the shape and alignment of a patient’s bones, intricately detailed plastic models are made with the 3D printer. The surgeons can then plan and practise conducting the surgery using the simulated bone structure.
3D printing not only shortens the time it takes to perform a surgery and therefore reduces the amount of blood lost, it also allows surgeons to shape the metal implant so that if fits perfectly before the operation. Especially for complicated and atypical surgeries, 3D printing can play an important role in surgical planning.
Tang recalls the case of 22-year-old patient in Shaanxi who lost his left leg after stepping on a landmine when he was seven. He says the patient underwent multiple operations over the past decade that resulted in many problems: his legs were different in length, he had weak bones and supporting tissues and there were injuries left by previous implants. After considering the surgical complexity, Tang used 3D printing technology to make a plastic model of the patient’s bad leg so the complex surgery could be practised in advance.. The actual surgery was a success. “The 3D model costs about HK$3,000 … Even if we get it wrong, we can try again. But we won’t have a second chance on the patient’s body,” he says.
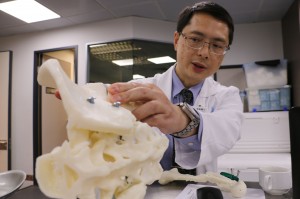
In another case, involving a pelvic fracture after a car accident, Tang found it would be dangerous to perform the surgery as there were complex blood vessels near the pelvis. Without 3D printing, doctors can only study the computerised tomography (CT) scans or 2D projections of a fractured bone. The real surgery itself is the first and only “drill” surgeons have. “We open a large wound in the surgery. While we take at least an hour to bend [the metal framework] into the patient’s body, the wound keeps bleeding,” Tang says. In the mock surgery using a 3D model, the surgeons can simulate the difficulties of the operation and familiarise themselves with the unique anatomy of each patient.
As the application of 3D printing in surgical planning develops apace, medical researchers and engineers are looking further ahead by asking whether 3D printing can be used to produce joints and bones to be implanted into the human body?
Professor Arthur Mak Fuk-tat, division head of biomedical engineering at the Chinese University of Hong Kong, believes one of the major future developments of 3D printing will be the manufacture of customised and patient-specific implants to replace traditional ones. He says that, for example, typically in operations to remove tumors from hip joint bones, Asian patients have to order implants from Europe. However, the size and curve of hip joints are different for Caucasians and Asians, leading to problems like the implant not matching perfectly with the Asian patient’s bone structure.
“It’s not just about size S, M and L… It will be harder for doctors to place the implant inside the bone marrow if the size doesn’t fit,” Mak says. He is hopeful that 3D printing can revolutionise the field, so that each implant is precisely designed and created for each patient. In August, surgeons at the Peking University Hospital in Beijing successfully replaced a section of spine of a 12-year-old bone cancer patient with a 3D-printed implant. This opened up possibilities of developing 3D-printed replacement bones.
Despite medical breakthroughs using 3D printing around the globe, there are still technical difficulties researchers like Mak have to solve. “3D printing which uses plastic can’t make artificial hip and limb joints. There is metallic 3D printing, but it’s very expensive,” he says. 3D-printing of metal and bio-compatible materials can cost millions of dollars, while the quality and non-toxicity of the implants printed cannot be guaranteed at this stage.
Before 3D printing can become a mainstream production method for biomedical devices, there has to be clinical observation of whether 3D-printed implants will harm patients’ health. “It can be devastating if the device breaks down in a human body,” says Mak, “but I think the problems will be resolved sooner or later, it’s just a matter of time. It’s a question raised but not a barrier.”
But for the medical application of 3D printing to really take off, Mak thinks there needs to be more private sector investment. Universities currently pioneer this kind of research, but it is important to have industrial partners to promote the technology. However, the risk of potential losses and the huge start-up funds needed put industrialists off. “Hong Kong industry still demands [to see] immediate benefit,” Mak sighs.
The Hong Kong Productivity Council (HKPC) has been involved in the research and application of 3D-printing technology, and may become a bridge between the innovators and the industry. Bryan So, principal consultant in the Biomedical Optical and Precision Engineering Division, says the council is working with doctors who conduct research on the technology to help commercialise their achievements and recommend possible business models. For example, HKPC has joined up with the University of Hong Kong to design artificial finger joints and introduce the designs to manufacturers. “This is a new business and we are still exploring the path to run it, but it will be a growth industry,” he says.
Apart from Hong Kong, many countries are stepping up their efforts to apply 3D printing into biomedical research and surgery. In May, Singapore’s Nanyang Technological University opened a US$30 million 3D printing research centre to conduct research on bone regeneration and bioengineering. It also signed a $5 million joint laboratory agreement with a German 3D printer manufacturer at the launch. Last year, a research team in the US managed to print parts of a functioning human heart with blood vessels. Scientists predict it will be possible to print an entire organ in three to five years and testing on humans will begin in less than a decade.
3D printing could turn elements of science fiction into reality. Hong Kong will need to redouble research efforts to keep up with the global advances in the technology if it wants to be part of what may evolve into a multi-billion dollar business that could also save lives.
Edited by Cindy Ng